What Happens When You Combine a Motor, ESC, and Propeller? IPET Just Showed Us
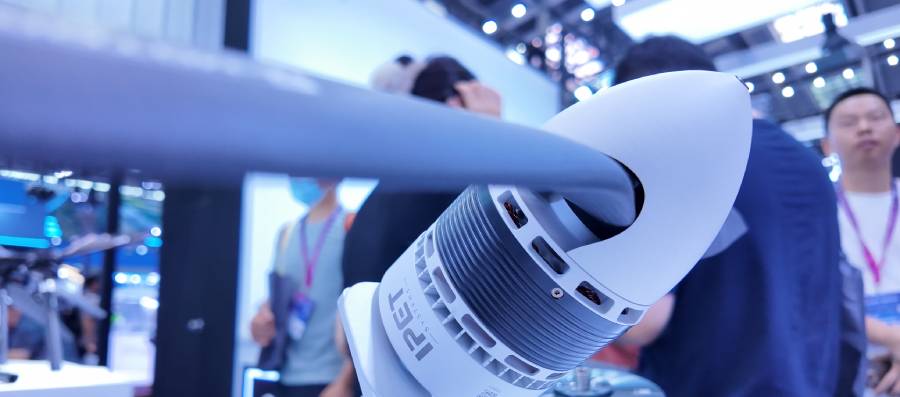
The more efficient, quieter, and reliable your motors are, the longer your flight, the bigger your payload, and the smoother your entire operation becomes. That’s where IPET System jumps in—a nimble, high‑tech company quietly reshaping the drone propulsion game for professional UAV users worldwide.
IPET, which stands for Integrated Electric Power Technology, builds high‑end power systems that blend motor, Electronic Speed Controller (ESC), and propeller into sleek, all‑in‑one units. It might not sound flashy, but this approach fixes countless hassles for operators—from complex wiring to routine maintenance issues—and ramps performance in nearly every category. This is enterprise drone engineering done right.
Founded by engineers with more than a decade working directly with drone propulsion tech, IPET took feedback from thousands of real‑world users and started stripping away inefficiencies one by one. The result is a propulsion ecosystem that marries hardware and software seamlessly. Integrated design avoids matching problems between separate components. Built‑in health monitoring keeps tabs on motors in flight. Quick‑release propellers mean field maintenance without tools. And most impressive of all, these units operate up to 10x longer than legacy systems.
Take their standout model, the I7. It’s built for serious airborne missions—think longer inspections, delivery, and public safety work. With a maximum takeoff weight (MTOW) of around 16 kg and a 2‑hour in‑air endurance, it delivers serious performance. More than that, the system has been pressure‑tested through accelerated aging for over 10,000 flight hours, positioning it as a durable option for continuous, industrial‑grade work. And the icing on the cake? Integrated thermal management and noise‑reducing prop design that keeps these heavy‑duty motors surprisingly quiet.
What’s remarkable is how these systems address real pain points. Swapping props traditionally takes time and tools, but IPET’s quick‑release design allows a change in just a couple of seconds—no hex wrenches required. That adds up when you’re flying in the field and need fast turnaround before conditions shift. Plus, having ESC and motor optimized together guarantees smoother power delivery, better efficiency, and fewer points of failure.
Their product lineup includes the I‑Series and I‑Series IV, both featuring integrated units tailored for multirotor and VTOL drones. These are enterprise‑level products—aliased for inspection, surveying, mapping, maritime, delivery, public safety, and BVLOS flights. IPET is carving out a strong niche: providing professional drone operators with propulsion they can trust under pressure.
On the global stage, partnerships are already forming. The I7 is drawing attention from ARTCOPTER in Korea, and demand is spreading across Europe, North America, Australia, Saudi Arabia, and beyond. That surge comes from IPET focusing on manufacturing quality, complete system thinking, and high‑level customer support by engaging with distributors keen to bring professional drone solutions to local markets.
IPET’s advantage lies not just in hardware. Every unit collects telemetry for health monitoring. Clients can watch motor temps, power output, and even detect AD anomalies before they become flight‑critical. This proactive mindset reduces maintenance costs, prevents mid‑air failures, and maximizes drone uptime—key advantages for enterprise clients managing large drone fleets in mission‑critical operations.
A quieter drone isn’t just neighbor‑friendly; it means reduced noise disturbance on sensitive job sites—like wildlife areas or police operations—and helps meet noise regulations. By designing propellers that cut decibels without compromising thrust, IPET addresses a subtle but important part of professional drone deployment.
Behind the scenes, IPET embraces test‑driven design. Their systems endure extreme environments: temperature cycles, humidity, repeated starts and stops, endurance runs. This isn’t lab marketing—it's real‑world resilience testing under stress. Hitting the 10,000‑hour mark is not just bragging rights—it makes these units justifiable investments for operators who fly year‑round.
IPET makes power systems that aren’t simply add‑ons—they’re full‑scale propulsion solutions. Each component is tuned to work in concert: Motors and ESC are matched, propellers optimized for each unit’s RPM and thrust curve. This efficiency doesn’t just improve flight time—it raises payload and reduces carbon emissions. For operators running inspection missions across miles of powerlines, pipeline, or coastline, those extra minutes and extra kilograms of payload can be game‑changing.
Looking ahead, IPET’s designs fit into bigger ecosystems. BVLOS (Beyond Visual Line Of Sight) operations, drone delivery routes, autonomous inspection flights—they all demand propulsion that’s predictable, connected, and remotely monitored. IPET’s health‑aware systems slot neatly into these digital logistics networks. As urban airspaces and drone corridors develop, hardware that’s smart and safe by design will set industry standards.
Some skeptics worry: do operators really need integrated motor‑ESC‑propeller units? It’s a fair question for hobbyist or light‑use drones—but IPET is targeting enterprise users, where every detail matters. Fewer cables, fewer failure points, cleaner installs, smarter diagnostics—these reduce operational risk and maintenance load. When regulators, insurers, and auditors look at your UAV systems, integrated systems with health logs are much easier to certify and maintain. That counts when drones are part of public safety or infrastructure monitoring workflows.
IPET’s ascendancy is a testament to thinking big about small tech. They didn’t just tweak existing drone motors—they re‑architected the propulsion stack. And the real‑world validation is rolling in: growing distributor interest, pilot deployments, and rising industry buzz suggest they’re onto something big.
Whether it’s a utility operator scanning kilometers of powerlines, a public safety crew responding to emergencies, or a logistics fleet moving goods by drone, IPET’s mission is clear: reliable, efficient, quiet, and smart propulsion at scale. With their I7 and I‑Series systems, they’re electrifying enterprise UAVs—pushing flight times to two hours, service lifespans to 10,000 hours, payloads past 2 kg, and noise well below expectations.